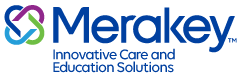
Job Information
Killdeer Mountain Manufacturing, Inc Quality Team Supervisor in Dickinson, North Dakota
About KMM
Killdeer Mountain Manufacturing is an award winning, Tier 1, manufacturer of electronic components for military and aerospace industries. With facilities in Dickinson and Killdeer, North Dakota, and Kerrville, Texas, KMM is committed to excelling in realms of our operations as well as commitment to community, country, and family!
JOB SUMMARY
The purpose of this position is to provide guidance and support to the Quality Department responsibility and to provide a work environment where coworkers have the tools, training and leadership to build a quality product and become effective Quality Inspectors. The QA Team Lead's goal is to assist in improving profits and cash flow through process improvements and ensuring the highest quality product is being delivered to the customer.
The QA Team Lead will conduct themselves in a professional manner and at all times be responsive and respectful.
Perform all tasks involved within Quality Assurance. This includes but is not limited to the duties and responsibilities listed below.
ESSENTIAL JOB FUNCTIONS
Current knowledge of customer requirements and industry standards.
- Continuously aware of customer specification changes/updates.
- Research, investigate, and interpret customer specifications, drawings, and related procedures/instructions.
Ensure that all First Article Inspection (FAI) requirements are being met. This includes completing FAI forms and documentation.
- Per AS9102 - Aerospace First Article Inspection Requirement.
Communicate all quality issues to the Quality Manager(s).
Monitor inspection results (First Pass Yield) to identify possible quality trends, both positive and negative.
Implement and maintain a Quality improvement plan that successfully identifies the root causes of matters pertaining to quality and ensures alignment of plan to KMM Quality department goals and strategies.
Monitor and ensure adherence to company policies, procedures, and customer requirements and take steps necessary to address compliance issues.
Monitor and report Quality Assurance scheduling and personnel issues.
- Develop and maintain the Quality Assurance Training Matrix.
- Assist Receiving and Final Inspection as needed.
Understand and apply KMM Root Cause Corrective Action disciplines by assisting and where required, facilitate internal and external Corrective/Preventative Action activities.
- KMM-025 Corrective-Preventive Action
Perform Audits and Verifications when required.
Communicate effectively and respective with Production Team Leads, Operators, Trainer, Manufacturing Engineers, Program Manager, Quality Manager, and Source Inspectors/Customer Representatives.
Must be willing to take a lead role in team problem solving and continuous improvement projects.
This position requires a certain level of independence and self-assurance as oftentimes decisions are required without the opportunity for conclusion with immediate supervisors.
Wear appropriate personal protective equipment as required by job task.
Adhere to all KMM safety policies and practices as well as manufacturer recommendations on operation of all equipment and tools
Assist with LEAN manufacturing by becoming a leader and assisting with the following:
- Teach, Coach, Mentor
- Serve as facilitator for Lean initiatives in their area
- Help identify process improvement ideas and identify metrics
- Work with KMM Lean Liaisons to compile metrics
- Keep their Liaisons and Practitioners informed on projects
- Coordinate Lean training for their area
Performs other related duties and assignments as required.
This individual has the responsibility and authority to carry out assigned tasks
This individual will be involved with the FOd prevention committee and may be asked to take on the role of FOd focal as necessary. The FOd focal responsibilities are outli