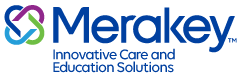
Job Information
Cambrex High Point Process Engineer 2 in High Point, North Carolina
Company Information
You Matter to Cambrex.
Cambrex is a leading global contract development and manufacturing organization (CDMO) that provides drug substance, drug product, and analytical services across the entire drug lifecycle. With more than 40 years of experience and a growing team of over 2,400 professionals servicing global clients, Cambrex is a trusted partner in branded and generic markets for API and dosage form development and manufacturing.
Your Work Matters.
At Cambrex, we strive to build a culture where all colleagues have the opportunity to:
engage in work that matters to our customers and the patients they serve
learn new skills and enjoy new experiences in an engaging and safe environment
strengthen connections with coworkers and the community
We’re committed to attracting and nurturing a passionate team of valued professionals in our fast-paced and growing company. We offer a competitive benefits package that includes medical, dental, vision, Life, LTD, retirement savings and more!
Your Future Matters.
Known for our customer-focused scientific and manufacturing excellence, as well as our strong commitment to quality and safety, we offer a range of career and growth opportunities across our global network of locations. Together with our customers, we aim to improve the quality of life for patients around the world. Start a career where You Matter by applying today!
Job Overview
The Process Engineer 2 will be responsible for implementation of projects for the manufacture of APIs and bulk intermediates and other products from development through piloting and/or commercial production.
Responsibilities
Composing batch production records, cleaning records, SOPs, campaign reports, supplements, and investigation/deviation reports as needed to support production operations
Identifying and monitoring KPIs and using process data to identify and execute improvements to new and existing products to achieve improved yields, quality, or customer expectations
Working with Process Improvement resources where applicable to drive optimization of production
Providing targeted training and process support to production areas, including training on new processes, as well as on-site oversight of key processing steps
Working in a team environment that includes cross-departmental participation from Facilities, Chemical Research and Development, Regulatory, Quality Control, and Analytical Research and Development
Developing plans and process fits for production
Developing and maintaining IQ, OQ and PQ documents and protocols
Leading and coordinating troubleshooting efforts where appropriate, investigating process problems and deviations, and preparing appropriate reports on findings
Participating in HAZOPs and other S&IH reviews, and providing guidance on corrective actions when needed
Where required, providing PFDs, energy balances, material balances, environmental calculations, and other pertinent production information
Working with appropriate departments to set up codes, label requests, and MSDS revisions
Completing CAPAs and audit action items as assigned
Qualifications/Skills
Ability to integrate information from diverse areas/sources and independently develop creative solutions
Excellent verbal and written communication and interpersonal skills, problem-solving, and organizational skills
Demonstrated ability to work in a diverse team environment
Proficiency with Microsoft software (Word, Excel, PowerPoint)
Exposure to broader analytical techniques (i.e., beyond USP compendial testing). Some supervisory experience
Experience / proficiency with various information and documentation software (SAP, TrackWise, etc.)
Leads with Integrity and Respect; Delivers Results; Demonstrates Business Acumen; Fosters Collaboration and Teamwork; Champions Change; Engages an d In spires; Coaches and Develops
Education, Experience & Licensing Requirements
BS in Chemical Engineering, plus 3 - 7 years of experience in a manufacturing environment, preferably in pharmaceutical manufacture; or equivalent education/experience
Knowledge of and/or direct experience in a cGMP environment is preferred
General knowledge of chemical operations equipment and manufacturing operations
#CB
#LI-RD1
Some active work, exerting up to 50 pounds of force occasionally, and/or the amount of force frequently or constantly to lift, carry, push, pull or otherwise move objects. The daily work is performed is primarily in a production setting. Walking and standing are required regularly.
Use of ladders and roof access may be required.
Position also requires visual acuity, talking and fingering.
Involves regular use of basic PPE (personal protective equipment) such as supplied air respirator, negative pressure respirator, gloves, safety glasses, shielding clothing.
A Chemical Manufacturing environment. Basic hazards associated with a small chemical plant environment such as: flammables and/or toxic materials, heavy item movement, large machinery operation.