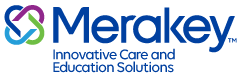
Job Information
TOLMAR Inc. Manager Equipment Automation in Windsor, Colorado
Purpose and Scope The Automation Manager is responsible for the overall management of automation engineering activities at all Tolmar locations.
Essential Duties & Responsibilities Manage the Automation Engineering team and manage related contractor resources. Coordinate with internal partners and external vendors to ensure timely execution of automation activities. Develop and implement standardized metrics that guide actions and promote continuous improvement. Drive improvement to latest automation technologies, ensuring reliability and throughput in a rapid growth environment. Ensure the development and retention of a high performing team to meet the current and evolving needs of the business through effective selection, training, coaching/mentoring, and performance management. Communicate with regulatory agency representative as automation expert during audits and defend investigation, changes, and current practices. Create strategic projects to ensure that the life cycle management of automated systems is appropriate and complete. Responsible for collaborating with the MRO coordinator to maintain spare parts inventory for assigned equipment, including monitoring levels, initiating requisitions, completing budget review, and ordering necessary materials. Assist with quality event investigations and company audits. Assist in facility layout and design for newer process areas and expansions for automation equipment and instruments. Contract with outside service providers for various automation facility and equipment-related needs. Provide engineering expertise and direction to employees and contractors to meet project deadlines and financial goals while ensuring technical success. Responsible for engineering support and maintaining equipment and processes to include the construction, modification and improvement of equipment utilizing direct reports. Responsible for maintaining content of training records for department in compliance with cGMP standards. Develop and maintain successful working relationships with both internal and external clients. Assist management with preparation of budget for department and monitor adherence to budget. Ensure the department's compliance to established company safety policies and procedures. Perform other duties as assigned.
Knowledge, Skills & Abilities Working knowledge of current Good Manufacturing Practices (cGMP) and ISO 9001 equipment requirements. Experience managing automation systems in an FDA-regulated manufacturing setting. Working knowledge of PLCs, HMIs, Data management and SCADAs (iFix/Wonderware) to support systems: design, programming, maintenance. In-depth knowledge of automation, control systems, and computer system (e.g. Rockwell Automation, Honeywell EBI, Delta Controls Orcaview, and JCI Metasys Building Management Systems (BMS). Experience preparing project budget and timelines. Knowledge of GMPs, FDA guidelines, purchasing practices, and qualification requirements. Knowledge of calibration functions in a FDA regulated facility. Strong managerial skills, coupled with excellent oral and written communication skills. High mechanical aptitude; ability to analyze the mechanics of new equipment for the most efficient outcome. Overall technical competencies necessary to manage and direct skilled maintenance technicians. Procedure writing and review skills. Computer skills include Word, Excel, and PM scheduling. Demonstrated ability to work efficiently under conditions of multiple deadlines and changing priorities in production. Ability to problem-solve a broad range of technical issues. Ability to plan and work with supporting technical resources such as internal engineers and scientists as well as contract support and external suppliers and consultants.
Core Values The Automation Manager is expected to operate within the framework of Tolmar's Core Values: Consistently operate with the highest sta dards of ethics and compliance. Take ownership of your actions, success and setbacks. Respect each other and understand that honest collaboration is at the heart of our company success. Go the extra mile to make things happen. Be committed to all we do and the patients we serve. Embrace change with enthusiasm. Strive to learn about and understand the needs of customers and patients, and take action with great speed and efficiency no matter the task.
Education & Experience Bachelor's degree preferred, or equivalent combination of education and experience. Five or more years of automation and calibration experience in a regulated industry, preferably in the manufacture of sterile drug products and/or medical devices. Two or more years of supervisory experience preferred. Experience utilizing an automated PM scheduling, work order, spare parts, and calibration software package (Maximo preferred). cGMP audit management experience preferred.
Working Conditions Manufacturing environment including general manufacturing and aseptic process areas. May require occasional weekend and/or evening work.